Center for Skill and Entrepreneurship Development - Smart Manufacturing
Industry Inside Institute
The Center of Excellence in Smart Manufacturing within an academic institute serves as a dynamic hub for integrating advanced manufacturing technologies with cutting-edge research and education. This center fosters collaboration between industry and academia, driving innovation in areas like automation, IoT, AI, and data analytics. By offering a hands-on environment where students, faculty, and industry professionals can work together on real-world projects, the center bridges the gap between theoretical knowledge and practical application. It plays a crucial role in developing the next generation of skilled professionals, enhancing industry capabilities, and contributing to the growth of smart manufacturing practices on a global scale.

Product Design and Development

CNC Machining

Additive Manufacturing
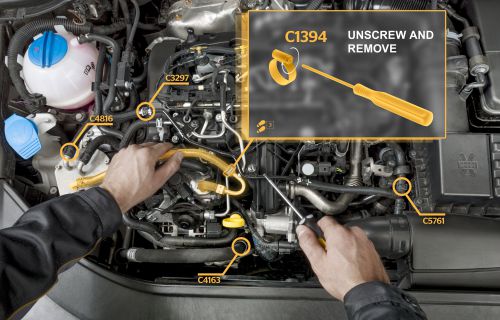
Virtual and Augmented Reality

Industrial Robotic
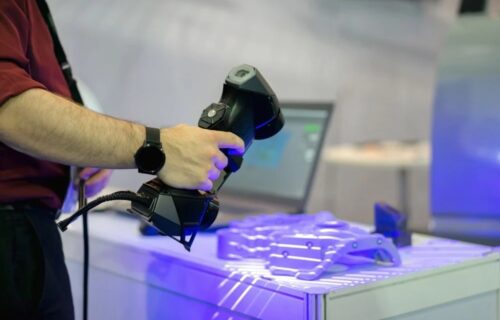
Reverse Engineering
OBJECTIVES
The objective of this training program is to equip learners with the knowledge and skills required to design and develop products using CATIA software.
OUTCOMES
- To give shape to the idea, concept design and controlling the geometrical shape of the designed component.
- To create 3D model of the design concept, understanding the part designing requirements that fulfil the design needs of various modules like CAE, CAM, CMM, Tool Designing, Drafting, 3D Printing.
- To understand , create, and control the complex shape geometries. To design & develop a new product from the existing one.
- To design assemblies, mechanism for validation.
- To understand the industrial drafting standards and generating industrial
SCOPE
- Design and Development Engineers,
- Product Development Engineer,
- Entrepreneurship
PROJECTS
- New product development
- Converting existing 2D drawings to 3D Model
- Delivery of Manufacturing drawing
Content

OBJECTIVES
The objective of this training program is to provide participants with a comprehensive understanding of the Computer-Aided Manufacturing (CAM) parameters for milling and turning using Mastercam software. This program will enable participants to gain practical knowledge and skills required to operate CNC machines effectively and efficiently. The program will focus on various aspects of CAM parameters, including feed and speed, toolpath, tooling, workpiece and fixture, machine, process planning, and quality control parameters.
OUTCOMES
- Understand the basic concepts of CAM parameters and their role in CNC programming and machine control for milling and turning operations.
- Calculate and optimize feed and speed parameters for different materials and cutting tools used in milling and turning operations.
- Select and optimize toolpath parameters for specific milling and turning operations and materials.
- Select and optimize cutting tools for specific milling and turning operations and materials.
- Optimize workpiece and fixture parameters for specific milling and turning operations.
- Optimize machine parameters for specific milling and turning operations.
- Optimize process planning parameters for specific milling and turning operations and materials.
- Implement quality control parameters for specific milling and turning operations and materials.
- Work on a real-world manufacturing project using both milling and turning operations.
- Geometric tolerance
- Understanding process planning
SCOPE
Upon completing this training program, participants can explore various job opportunities in the manufacturing industry, including CNC operator, CNC programmer, manufacturing engineer, quality control engineer, and production supervisor. The participants can work in various manufacturing sectors such as automotive, aerospace, defense, medical devices, consumer goods, and other manufacturing industries.
- Manufacturing Engineers
- CAM Engineer
- CNC Operator
- Entrepreneurship
PROJECTS
- Tool Manufacturing
- Converting existing 2D drawings to 3D Model

OBJECTIVE:
The objective of this program is to equip participants with comprehensive knowledge and skills in designing, implementing, and managing integrated automation systems commonly used in manufacturing facilities. Participants will gain proficiency in conveyor systems, sorting units, handling units, assembly units, automated storage and retrieval systems (ASRS), control cabinets, human-machine interfaces (HMI), and industrial robotic arms.
OUTCOMES:
- Understanding of the principles and functionalities of various automation components.
- Proficiency in designing and configuring conveyor systems, sorting units, handling units, assembly units, ASRS, control cabinets, and HMIs.
- Ability to integrate different automation units into a cohesive and efficient system.
- Competence in programming and controlling industrial robotic arms for diverse manufacturing tasks.
- Capability to analyze, troubleshoot, and optimize integrated automation systems for improved performance and productivity.
SCOPE:
- Introduction to Automated Manufacturing
- Conveyor Unit
- Sorting Unit
- Handling Unit
- Assembly Unit
- ASRS Unit
- Control Cabinet and HMI
- Industrial Robotic Arm
PROJECTS:
Participants will engage in hands-on projects to reinforce their learning, including:
- Designing and simulating a conveyor system layout for a manufacturing facility.
- Implementing a sorting unit to classify different types of objects based on predefined criteria.
- Programming a robotic arm to perform pick-and-place tasks in an assembly line setup.
- Integrating multiple automation units to create a functional production line prototype.
- Troubleshooting and optimizing an existing automation system to improve efficiency and throughput.

OBJECTIVES
The objective of this training program is to provide participants with comprehensive knowledge and practical skills in Knowledge Base Engineering (KBE). Participants will learn how to develop and utilize knowledge-based systems to automate engineering design processes, enhance productivity, and improve decision-making in various industries.
OUTCOMES:
Upon completion of the training program, participants will:
- Understand the fundamental principles and concepts of Knowledge Base Engineering.
- Be proficient in developing knowledge-based systems using appropriate KBE methodologies and tools.
- Learn to capture, represent, and manage engineering knowledge effectively within a knowledge base.
- Gain hands-on experience in implementing KBE solutions to automate design tasks and workflows.
- Demonstrate the ability to analyze and evaluate the effectiveness of KBE applications in real-world engineering scenarios.
- Collaborate effectively with multidisciplinary teams to integrate KBE solutions into existing engineering processes.
JOB SCOPE:
Professionals trained in Knowledge Base Engineering can engage in a variety of roles and tasks, including:
- Developing and maintaining knowledge-based systems for engineering design and analysis.
- Collaborating with domain experts to capture and formalize engineering knowledge.
- Implementing rule-based and constraint-based reasoning mechanisms to automate design tasks.
- Integrating KBE solutions with CAD/CAM software and other engineering tools.
- Providing technical support and training to end-users on KBE applications.
- Contributing to research and development efforts to advance KBE methodologies and technologies.
PROJECTS:
Participants will undertake a series of projects to apply their KBE skills in practical scenarios, such as:
- Designing and implementing a knowledge-based system to automate a specific engineering design process.
- Developing a rule-based inference engine to assist engineers in decision-making tasks.
- Creating a knowledge base for a complex engineering domain, incorporating both explicit and tacit knowledge.
- Collaborative project with industry partners to address a real-world engineering challenge using KBE techniques.
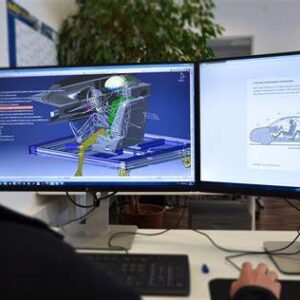
OBJECTIVE:
The objective of this training program is to equip participants with the knowledge and skills necessary to develop and deploy industrial AR solutions using Vuforia tools. Participants will learn about the different Vuforia tools available and how to effectively use them to create AR experiences for various industrial settings. The program aims to provide participants with hands-on experience in designing and building AR applications and enable them to explore the potential of AR technology in the industrial sector.
OUTCOMES:
- Understand the fundamentals of AR technology and its applications in the industrial sector.
- Utilize Vuforia Instruct, Expert Capture, Studio, Engine, and Chalk to create AR solutions for different industrial settings.
- Develop step-by-step work instructions, procedures, and training modules using Vuforia Instruct and Expert Capture.
- Design AR experiences using Vuforia Studio and integrate 3D models, animations, and multimedia assets.
- Build AR applications using Vuforia Engine and integrate with other development tools and technologies.
- Collaborate remotely and communicate in real-time using Vuforia Chalk.
- Evaluate the usability and effectiveness of AR applications in industrial settings.
- Develop effective maintenance and support strategies for AR solutions.
SCOPE:
Upon completion of this training program, participants will be equipped with the knowledge and skills necessary to pursue careers in the field of industrial AR. Job opportunities include roles such as AR Developer, AR Designer, AR Engineer, AR Consultant, and AR Project Manager. Companies that employ industrial AR include manufacturing, aerospace, defense, automotive, healthcare, and logistics.
PROJECTS:
Participants in this training program will work on various projects to gain practical experience in creating AR solutions for industrial settings. These projects will include developing step-by-step work instructions, procedures, and training modules using Vuforia Instruct and Expert Capture, designing AR experiences using Vuforia Studio, building AR applications using Vuforia Engine, and collaborating remotely using Vuforia Chalk.
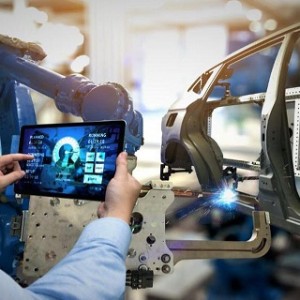
OBJECTIVE:
- Introduce students to virtual reality technology and its applications.
- Teach students the fundamentals of CATIA software and its use in creating 3D models.
- Develop students’ ability to create interactive VR experiences using CATIA and the HTC headset.
- Prepare students to design and develop VR applications for a variety of industries.
OUTCOMES:
- Introduce students to virtual reality technology and its applications.
- Teach students the fundamentals of CATIA software and its use in creating 3D models.
- Develop students’ ability to create interactive VR experiences using CATIA and the HTC headset.
- Prepare students to design and develop VR applications for a variety of industries.
SCOPE:
- Virtual reality developer
- VR design engineer
- VR software developer
- VR project manager
- VR consultant
PROJECTS:
- Designing a virtual reality showroom for a car manufacturer
- Developing a virtual reality training program for a manufacturing company
- Creating an interactive VR game
- Designing a virtual reality experience for a museum exhibit
- Developing a VR simulation for a medical device manufacturer

OBJECTIVE:
The objective of this program is to provide participants with comprehensive training in sheet metal design and basic tool development using the 3D Experience platform. Participants will learn essential techniques for creating sheet metal parts, designing tools for manufacturing processes, and leveraging the capabilities of 3D Experience software for efficient product development.
OUTCOMES:
- Proficiency in creating sheet metal parts including bends, flanges, and cutouts using 3D Experience.
- Mastery in designing basic tools such as dies and molds for sheet metal fabrication processes.
- Ability to optimize designs for manufacturability, cost-effectiveness, and efficiency.
- Competence in leveraging collaborative features of 3D Experience for team-based design projects.
- Capability to translate conceptual designs into detailed, production-ready models.
SCOPE:
The program will cover the following key areas:
- Introduction to Sheet Metal Design:
- Sheet Metal Part Design:
- Tool Development Basics:
- Advanced Sheet Metal Features:
- Tool Design for Sheet Metal Processes:
- Collaborative Design and Data Management:
PROJECTS:
Participants will engage in hands-on projects to reinforce their learning, including:
- Designing a simple sheet metal bracket using basic features in 3D Experience.
- Developing a progressive die for stamping a sheet metal part.
- Creating a mold for casting a basic sheet metal component.
- Collaborative design project involving multiple participants working together on a complex sheet metal assembly.
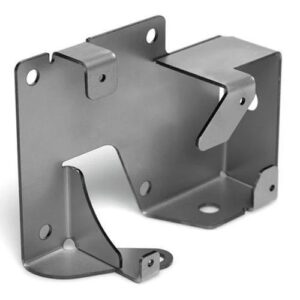
OBJECTIVE:
The objective of this program is to train participants in the process of reverse engineering using a Blue Light Scanner and Catia software, and subsequently utilizing the obtained data for 3D printing via FDM (Fused Deposition Modeling) technology. By the end of the program, participants will have acquired comprehensive skills in reverse engineering, CAD modeling, and additive manufacturing techniques.
OUTCOMES:
Proficiency in operating Blue Light Scanner equipment for capturing precise 3D data of physical objects.
Mastery in utilizing Catia software for reverse engineering purposes, including surface reconstruction and parametric modeling.
Ability to optimize scanned data for compatibility with 3D printing processes.
Competence in operating FDM 3D printing machines, including material selection, slicing, and post-processing.
Capability to integrate reverse engineering techniques with additive manufacturing for prototyping and product development purposes.
SCOPE:
Introduction to Reverse Engineering, Equipment overview and setup, Advanced modeling techniques, FDM technology overview
PROJECTS:
Participants will engage in hands-on projects throughout the program, including:
- Reverse engineering a mechanical part using Blue Light Scanner and reconstructing it in Catia.
- Designing a custom component based on scanned data and optimizing it for 3D printing.
- Prototyping a product concept through the integration of reverse engineering and additive manufacturing techniques.
- Collaborative project work focusing on real-world applications such as automotive parts, consumer products, or medical devices.
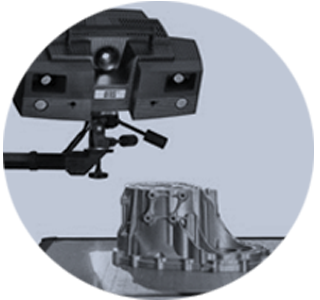
OBJECTIVES
The objective of this training program is to provide participants with the skills and knowledge required for styling Class A surface design, which is the highest level of surface quality in the automotive and industrial design industry. Participants will learn the principles, techniques, and tools used in creating high-quality, aesthetically pleasing, and functional Class A surfaces for various product design applications.
OUTCOMES
- Understand the concepts and principles of Class A surface design.
- Apply advanced surfacing techniques using industry-standard software such CATIA.
- Create Class A surfaces with precision, continuity, and curvature control GO, G1, G2 & G3.
- Understand the importance of design intent, reflections, and highlights in Class A surfaces.
- Identify and troubleshoot common issues in Class A surface modeling.
- Collaborate effectively with other design professionals in a multidisciplinary team environment.
- Develop a professional portfolio of Class A surface design work.
- Conceptual design of automotive Class A surface & CAD model of EV.
- Get idea of nurbs & slab modeling, sharp surface models.
- Surface evaluation – reflection lines
SCOPE
Graduates of this training program will have the skills and knowledge to work as Class A surface designers in various industries such as automotive design, industrial design, aerospace design, and consumer product design. They may find employment in design studios, product development firms, manufacturing companies, or as freelance designers. Job roles may include Class A surface modeler, automotive designer, industrial designer, product designer, or CAD modeler. Entrepreneurship.
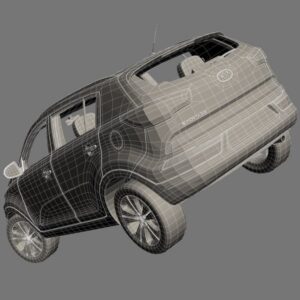