DCS Internet Of Things
There are more than 12 billion connected devices in the world—more smart “things” than people. We look at IoT as a driver of new forms of digital engagement—the collapsing boundary between physical and virtual. Innovative companies are adopting IoT strategy and technology to rethink their products and services and redefine their relationships with customers, employees and partners.
DCS’s view is that creating successful digital experiences requires expertise in digital strategy, foundational technologies, design and process and systems.DCS’s team with expertise in provides digital design solution can create end-to-end experiences that make up the fabric of this new form of engagement. Making digital experiences valuable requires that new flows of data get converted into business insight for meaningful action.

Smart Connected Products
IoT Is Shaping the Future of Customer Experience and Product Development”

The Digital Twin
Bridging the Physicaland Digital Worlds, the 21st-century approach to productivity enhancements.
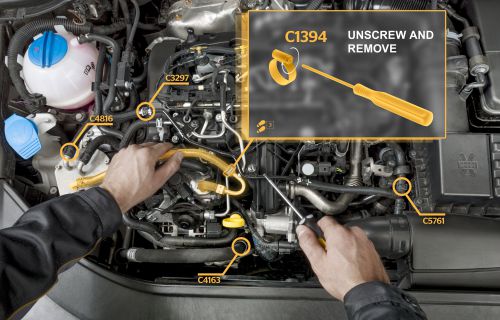
Augmented reality
(AR) is a live direct or indirect view of a physical, real-world environment whose elements are augmented
Our Services include
DCS partners with PTC to identify IoT business cases and put into place the technology to create entirely new business models and revenue streams, while reducing costs and boosting efficiency.
Connected Product Usage Analysis – Analyze and benchmark product performance and usage data collected through remote connectivity with sensor-equipped products or systems to inform and improve product requirements definition, prioritization of features, options and variants, life cycle costs, and supply chain coordination and planning.
Connected Product Quality Analysis – Continuously analyze field data collected through remote connectivity with sensor-equipped products or systems to improve root cause analysis and corrective actions, product quality, reliability and safety, preventative maintenance, and service.Connected
Software Management – Remotely identify and manage the as-maintained configuration of fielded products, systems and assets; control and automate the release of software updates and security patches by securely distributing packages of software files and instructions remotely.
Common IoT Metrics for Product Development:
- Shortened time to market
- Improved product failure rate (e.g. MTBF, mean time between failure)
- Reduced number of recalls, warning letters, and audits
- Reduced product development and product costs
- Improved equipment up-time and product quality
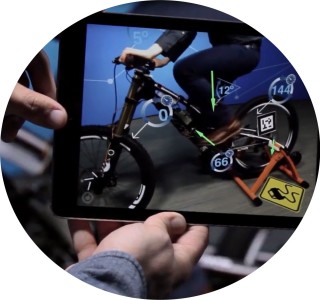
Asset and Material Tracking – Easily locate and monitor key assets (e.g. raw materials, final products, and containers) to optimize logistics, maintain inventory levels, prevent quality issues, and detect theft.
Connected Operations Intelligence – Connect disparate silos of operational data (e.g. manufacturing, supplier, and logistics) into unified, real-time visibility across heterogeneous systems, people and assets to make faster and better decisions and improve operational performance.
Unified Key Performance Indicators – Aggregate and contextualize data from isolated manufacturing systems and assets into actionable web and mobile applications that provide role-based views into key indicators, while also allowing drill-down into correlated data to diagnose problems more quickly and improve performance.
Real-Time Asset Health Monitoring – Minimize downtime and avoid potential equipment failures by enabling detailed monitoring of critical equipment condition and operating parameters to automatically trigger alerts and proactively initiate response from maintenance teams or OEM service networks when problems are detected.
Operations Management Improvements – Quickly improve how complex processes are monitored, managed, and optimized, and accelerate smart factory and Industry 4.0 initiatives, by extending existing equipment and ERP/MES systems with connectivity, interoperability, mobility, and crowd sourced intelligence.
Common IoT Metrics for Operations and Manufacturing:
- Reduced write offs of from missing and damaged assets or stock
- Improved product failure rate (e.g. MTBF, mean time between failure)
- Reduced number of recalls, warning letters, and audits
- Reduced manufacturing costs
- Manufacturing cycle time; overall equipment effectiveness
- Improved equipment up-time and product quality
- Product, asset, and equipment utilization rate
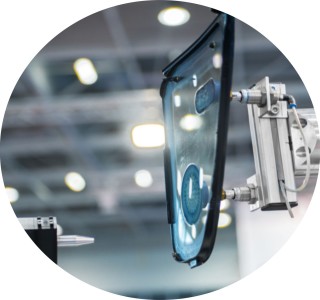
Monitoring and Diagnostics – Interact with connected products to identify and diagnose product issues remotely to eliminate unnecessary service calls and improve first time fix rate.
Remote Service – Interact real-time with connected products to perform remote service activities including machine adjustments, software updates, and self-tests to avoid downtime and eliminate need for on-site service calls.
Automated Service Execution – Automatically trigger service events based on connected product alerts, diagnose issues, determine the best service response and dispatch technicians based on SLA entitlements and resource availability.
Condition-Based Predictive Maintenance – Monitor connected product operating characteristics and combine with thresholds, trends, and analytics to move from reactive to proactive maintenance.
Connected Service Parts Planning – Leverage connected product data including configuration, utilization, and location to improve balancing of service level objectives with service parts inventory levels.
Warranty Cost Management – Continually monitor connected product usage to identify and prevent potential warranty compliance issues; automatically notify operator when compliance issues occur to avoid potential product failures and reduce warranty cost.
Common IoT Metrics for Service / Support:
- Reduced service costs
- Improve mean time to repair (MTTR); resolution time
- Service contract renewal rate
- Reduced warranty costs
- Reduce service events with no problem found
- Improve first time fix rate (FTFR)
- Increase service events avoided; remote fix rate
- Improve SLA compliance
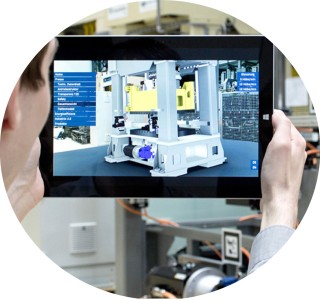
Connecting the sensors, devices and machines in the physical world to the Internet creates multiple new digital opportunities for industries, including:
- Life Sciences firms remote monitoring of clinical trials and medical devices
- Retailers creating more personalized in-store shopping experiences
- Banks providing better offers and more engagement via tellers and ATMs
- Manufacturers predicting when equipment will need maintenance
- Logistics firms designing real-time visibility into location and condition of assets
- Restaurants reducing customer wait times with “just-in-time” meal preparation
- Insurers increasing revenue through asset monitoring